Why Tiles Can Crack on New Build Developments?
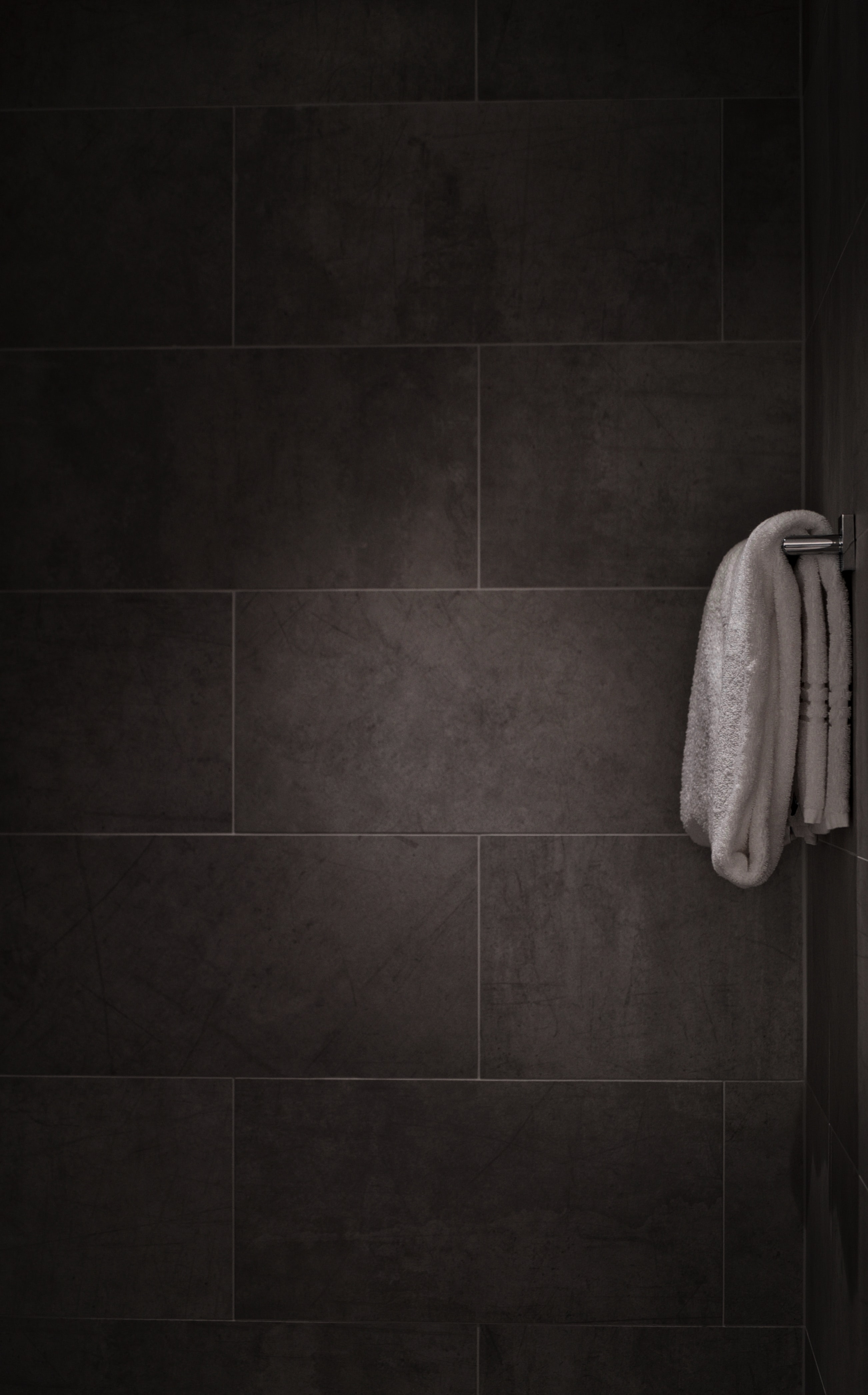
Tiles are a rigid, inflexible flooring and any cracks appearing are a reaction to another cause.It is common knowledge within the construction industry, that cracks that run in lines across several tiles or along grout joints are due to movement in the substrate and/or the building.Cracked tiles on a new development are obviously an undesired issue because they are visually unattractive as a floor finish and can pose as a future safety hazard. From a diagnostic perspective, we can view a tile crack as the first symptom of a larger issue. When some people see cracked tiles, they may initially assume that the tiles are faulty or have been incorrectly installed. The important point to understand is that these cracks are preventable, fixable and also a natural occurrence that can happen through substrate cracking by way of movement, settlement and/or subsidence of a new building. In this article we cover how to diagnose and solve the underlying problem of tile cracks, what can cause cracks in tiles on new developments, and how to prevent tile cracks from happening.
Specialist Ceramics are committed to providing the highest quality outcomes on all of our projects with foresight and expertise.
Identification of the Source
The assessment of a crack in individual tiles or a section of tiles usually starts with a visual inspection of the surface. It is important to take note on the location and nature of a crack, whether it is an extensive crack spanning the entire width of the room or cracks near a doorway entry. Identifying the exact source of a crack can be a difficult task given that the origin is typically caused by movement under the tile. However in most cases, an experienced tradesperson should be able to diagnose the problem with confidence after consideration of the building’s structural characteristics. Pinpointing the source of the crack usually requires a holistic perspective of building.
Solving the Problem
Solving the problem is matter that often requires input, expertise and collaboration between several different trades and professionals to make a judgement on how to address the issue.Naturally, the tile installers are involved in the problem solving process along with other parties which may include the engineer, architect, project manager or builder, concrete pourers, screed installers etc.The task of finding a solution to remedy the crack may require an investigative approach to reflect on the stages of the build to pinpoint the cause of the crack. There also needs to be an evaluation of the existing substrate to determine whether it is safe to replace the tile right away, because there is no point replacing the tile if there is potential for more movement in the building.In many cases, finding the source of the crack is a matter of removing tiles around the affected area, assessing the substrate and taking necessary preventative measures to address the issue before re-tiling the affected area.
What Can Cause the Cracks in Tile?
- Reflective cracking: When tile is bonded directly to a concrete slab and that concrete substrate cracks, this movement transfers onto the surface layer and often causes multiple tiles to crack. These cracks are typically long, continuous and extend along a stretch of tiles.
- Subsidence is downward movement of the building foundations and/or structural floor due to the change in volume of the supporting earth and soil. When subsidence occurs, it can cause minor or major cracking at multiple parts of the building. Doorways and windows are common areas that crack.
- Settlement is the normal settlement of the building into position after being constructed. During this process the building settles into a permanent position. Hence there is more room for movement and opportunity for the building to crack at different locations. Most of the settlement of a new building occurs within one to ten years after construction.
- Control Joint Cracking: In larger areas, the function of a control joint is used to control the cracking caused by movement in a concrete slab. Tiling over control joints without accounting for movement is another cause of cracking. Hence, it is important to transfer the same control/movement joints into the tiling at the exact same point.
- Concrete Substrate Below the Tile Did Not Cure: Concrete slabs need a sufficient amount of time to cure before tiles are installed. Installing tiles over uncured concrete can caused cracks to the tile. The length of time needed can depend on several factors such as the cement to aggregate ratio, particle size, water exposure, environmental factors and whether there are additives used to speed up the cure time. Once a slab has cured, it may safely be tiled over.
- Heavy impact by a dropped item or the impact of heavy loads have the ability to cause cracks on new developments. After-all, the transportation of heavy items throughout the building is a common occurrence from start to finish of a new construction.
- Excessive movement in the substrate will cause a crack that runs through several tiles in a roughly straight line. Eg. Joists that are spaced too far apart will allow for deflection in the subfloor. One must analyse the materials used for subfloors to determine whether they have been installed correctly to avoid excessive movement.
- Incorrect Installation is another unfortunate cause of failure in the tile industry. Bad practices such as improper adhesive application can cause voids, gaps and weakness under the tile. It is essential that the tiles have even coverage of adhesive with a suitable sized notch trowel to ensure the integrity and strength of the bond. Other forms of malpractice may include: tiling over an unsuitable or uneven substrate surface, avoidance of primer when required, use of unsuitable adhesives, incorrect spacing between tiles, no consideration for the expansion joints, inadequate screed installation and waterproofing failure, among other installation flaws that may be a product of carelessness, inexperience or installation shortcuts.
Prevention and Management of Cracks in Tile
Crack Isolation Membranes may be used on substrates to prevent future cracks prior to tile installation or as a way to treat the problem of an existing crack after damaged tiles have been removed. These membranes are designed to allow for movement of tile from the substrate, functioning to allow the tiles to move separately from the substrate and absorb any shock.
There is also the use of anti-fracture or decoupling mats to account for lateral movement (side-to-side) over areas that pose a potential risk of cracking. It is important to note that any vertical movement can still be transferred to the tile with the use of these mats.
Specialist Ceramics only use flexible, premium products to maximise product performance and flexibility against substrate movement. Bear in mind, that there are still limitations on how much cracking, shrinkage, or movement can be compensated by flexible products.
The use of movement joints (otherwise known as control joints or expansion joints) in large floor areas is another preventative measure. Ensuring that the tiling joints align with the existing control joints on the substrate is imperative to avoid any voids caused by substrate movement in larger rooms more than 10m x 10m. The use of a flexible silicone or pre engineered control joint at the expansion joint functions to allow for movement. The building designer should assess the magnitude of any stresses on floors and walls to decide where movement joints, flexible joints and contraction joints should be applied, with regard to the type of material used.
Perimeter floor joints function to separate the floor tile from walls or other vertical structural elements. They serve the same preventative purpose against cracking by accounting for movement of the substrate or tile after installation. A perimeter joint should at least account for6mm in width and reach the depth to the substrate or decoupling mat. For a professional finish, skirting is installed over the perimeter joint to provide an aesthetic finish, followed by the use of sealant or silicone at exposed joints.
Above all else, prevention of cracked tiles and general voids is a task that combines foresight, preparation, experience, and commitment to inspecting every project on a case-by-case basis. Whether it be inspecting or preparing the substrate for tiling, we like to plan ahead.
At Specialist Ceramics, we are accustomed to assessing the unique aspects of each project to prevent potential delays. When problems arise, we are always there to put our best foot forward to find the most suitable and cost-effective solution to any problem.